Why Choose Powder-Coated Chain Link Fencing? The Process and Benefits
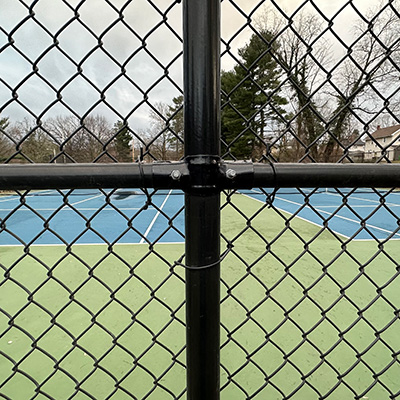
Powder coating is an advanced finishing process where a dry, electrostatically charged powder is applied to metal surfaces, such as chain link fences and fittings, and then cured under heat to form a protective, durable coating. Unlike liquid paint, which requires solvents, powder coating adheres to the metal using an electrostatic process before undergoing high-temperature curing, creating a hardened surface that resists wear and tear. But why is this important for chain link fences? Fences constantly face harsh environmental conditions, including moisture, UV rays, and temperature fluctuations. Powder coating enhances the fence's lifespan and reduces maintenance needs by preventing rust and corrosion. This process is eco-friendly, producing minimal waste and emitting fewer volatile organic compounds (VOCs), making it a more sustainable choice for residential and commercial fencing applications.
When choosing a finish for chain link fences, many wonder: is powder coating better than traditional liquid paint? The answer largely depends on durability, maintenance, and overall performance. Unlike conventional paint, which can chip, peel, or fade over time, powder-coated surfaces are significantly more resistant to physical and environmental damage. The electrostatic application method ensures a uniform and thicker coating, eliminating issues such as uneven coverage or drips commonly found in painted finishes. Additionally, powder-coated fences require little upkeep, as the finish resists scratching, fading, and rusting much better than paint. Another key advantage is aesthetics—powder coating allows various color options, textures, and smooth finishes that remain vibrant for years without frequent touch-ups. In short, powder coating is a superior alternative to traditional painting for those looking for a long-lasting, low-maintenance, and visually appealing fence finish.
What Can Be Powder-Coated? Chain Link Materials, Fabric, & Fittings
Not all materials are suitable for powder coating, as the process requires electrically conductive surfaces that can withstand high curing temperatures. Applying powder coating to these materials and components makes chain link fences more durable, low-maintenance, and customizable, making them an ideal choice for residential, commercial, and industrial applications. The most common materials and components used in chain link fencing that can be powder-coated include:
What Materials Can Be Powder-Coated?
- Galvanized Steel: One of the most popular fencing materials, galvanized steel can be powder-coated with proper surface preparation to ensure adhesion. The process adds an extra layer of defense against rust and corrosion.
- Aluminum: Naturally resistant to corrosion, aluminum components like posts and fittings can be powder-coated to enhance durability and achieve a customized finish.
- Wrought Iron: Used in decorative fencing or heavy-duty gates, wrought iron benefits from powder coating by preventing rust and extending its lifespan.
What Chain Link Parts Can Be Powder-Coated?
- Chain Link Mesh: The interwoven steel wires that form the main fence barrier can be powder-coated to resist corrosion, prevent oxidation, and add a smooth, protective finish.
- Posts (Line Posts & Terminal Posts): As the primary support structures, these steel or aluminum posts benefit from powder coating by gaining extra protection against rust, scratches, and UV damage.
- Fittings & Hardware: Small but essential parts like rail end cups, tension bands, post caps, clamps, and tie wires can also be powder-coated. This helps prevent premature wear and ensures a cohesive, long-lasting fence system.
- Gates & Frames: Powder coating adds an extra layer of strength and weather resistance to chain link gates, frames, and hinges, reducing the risk of rust and wear from frequent use.
Shop Black Powder-Coated Chain Link Fittings
Shop All Powder-Coated Fittings
The Powder-Coating Process Explained
Powder coating is a multi-step process that enhances chain link fencing components' durability, appearance, and weather resistance. Unlike traditional painting, this method creates a uniform, long-lasting finish without solvents. The process involves preparing the surface, applying the powder, and curing it under heat to form a strong protective layer. Each step is essential in ensuring the coating adheres properly and provides maximum protection against wear, corrosion, and environmental exposure. By following a precise application and curing process, powder-coated chain link fences achieve a durable, low-maintenance, and visually appealing finish suitable for various applications.
Part 1: Surface Preparation: Setting the Foundation for a Strong Finish
Before powder coating can be applied to chain link fence components, the metal surfaces must be meticulously prepared to ensure proper adhesion and long-term durability. If the surface is not adequately cleaned and prepped, the coating may not bond correctly, leading to peeling, chipping, or premature failure. The preparation process involves multiple steps to remove contaminants, create a suitable texture for adhesion, and improve corrosion resistance. These steps include:
- Sandblasting: This process uses high-pressure abrasive materials to remove dirt, rust, old coatings, and surface imperfections. By creating a slightly rough texture, sandblasting enhances the powder's ability to grip the surface, ensuring even coverage and stronger adhesion.
- Degreasing: Oils, grease, and other contaminants left from manufacturing or handling can interfere with adhesion. A chemical degreasing solution or a high-temperature alkaline cleaner strips these substances from the metal surface, leaving it clean and ready for coating.
- Phosphate Treatment: A chemical solution, usually zinc or iron phosphate, is applied to the metal to provide an additional layer of corrosion resistance. This process also enhances the metal's bondability with the powder coating, increasing durability.
Chain Link Cleaning Process
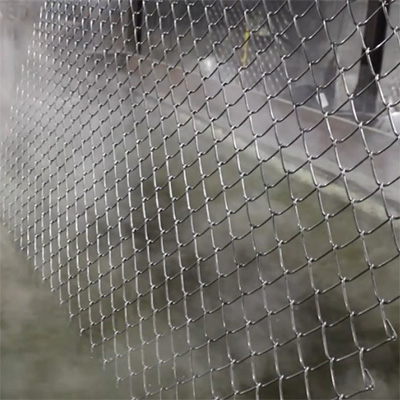
Part 2: Powder Application Techniques: How Does the Powder Coat Stick?
Once the surface is properly prepared, the powder coating is applied using one of two primary techniques, each designed to maximize coverage, durability, and efficiency. These methods ensure the powder adheres to the metal evenly and consistently before it undergoes curing.
Method 1: Electrostatic Spray Deposition (ESD)
- Uses a specialized spray gun to electrostatically charge powder particles, giving them a negative charge before spraying onto the positively grounded metal surface.
- This process ensures an even, controlled application with minimal waste and provides a uniform coating, even on complex shapes such as fence brackets, caps, and fasteners.
- The charged powder is attracted to all areas of the metal, reducing the likelihood of missed spots and ensuring thorough coverage.
- Once the powder has been applied, the coated piece moves to the curing oven for the final step in the process.
Method 2: Fluidized Bed Application
- In this method, metal parts are preheated to high temperatures and then dipped into a tank filled with a fluidized powder bed, where the powder melts and adheres to the surface instantly.
- This technique results in a thicker and highly durable coating, making it particularly suitable for industrial applications or high-wear components that require extra protection.
- Fluidized bed coating is often used for items that need an ultra-durable finish, such as high-impact fencing components or heavy-duty gates.
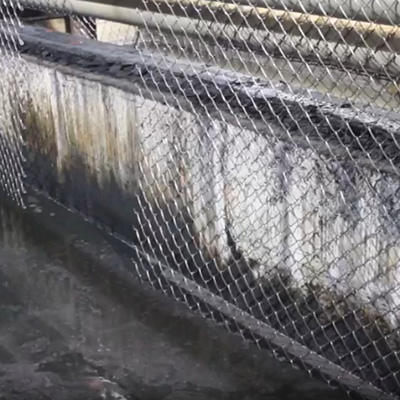
Part 3: Curing Process: Transforming Powder into a Durable Coating
After applying the powder, the coated components must undergo curing, transforming the powder into a hardened, protective finish. The coated parts are placed in a specialized curing oven and heated to temperatures between 300-500°F (150-260°C), depending on the type of powder used. The heat causes the powder particles to melt, flow, and chemically bond, forming a smooth, uniform film resistant to wear, impact, and environmental exposure.
Step 3.1: Placing Coated Components in the Curing Oven
The curing process begins with transferring the powder-coated components into a specialized curing oven that provides a controlled heat environment. The oven is preheated to a temperature between 300-500°F (150-260°C), depending on the specific powder formula. Proper positioning of the components is crucial to ensure even heat exposure, as inconsistent heating can lead to an uneven finish or defects in the coating.
Step 3.2: Melting and Fusing the Powder
As the components are exposed to heat, the powder particles melt and flow together, forming a uniform film over the metal surface. This step is crucial for thermosetting powders, which undergo a chemical cross-linking reaction that permanently hardens the coating. This reaction ensures the coating remains stable under extreme temperatures and outdoor exposure. On the other hand, thermoplastic powders melt and re-solidify upon cooling, making them more flexible but less heat-resistant over time.
Thermosetting Powders
- Undergo a chemical reaction during curing that permanently hardens the coating.
- Cannot be remelted or reshaped after curing, making them ideal for high-heat and UV-resistant applications.
- Common types include polyester, epoxy, and hybrid coatings, widely used for chain link fencing components due to their superior durability and weather resistance.
Thermoplastic Powders
- Do not undergo a chemical change during curing. Instead, they melt and solidify upon cooling, meaning they can be reheated and reshaped if needed.
- Offer high impact resistance but may soften under extreme heat, making them less suitable for long-term outdoor use.
- Often used in industrial coatings, but not as commonly applied to chain link fences due to their heat sensitivity.
For chain link fences, thermosetting powders (such as polyester and epoxy-based coatings) are the preferred choice, as they provide superior UV resistance, corrosion protection, and scratch resistance, ensuring the fence's longevity in various weather conditions. Thermosetting powders chemically react during curing and become permanently hardened, making them ideal for outdoor applications. Thermoplastic powders melt and re-solidify upon cooling, allowing for reheating and reshaping, but they lack the long-term heat and UV resistance needed for fencing.
Step 3.3: Ensuring Proper Curing Time
Once the powder has melted and adhered to the surface, the components remain in the oven for 10-20 minutes, allowing the coating to cure fully. The curing time depends on factors such as coating thickness, metal composition, and the type of powder used. Insufficient curing time can lead to soft or chalky coatings that may wear off prematurely, while over-curing can cause brittleness or discoloration. Precision in timing ensures the highest quality finish.
Step 3.4: Verifying Coating Quality
After curing, the coated components are carefully inspected to ensure the coating has adhered properly and formed a smooth, durable, and uniform surface. A properly cured finish is resistant to wear, impact, and environmental exposure. However, if the coating appears dull, uneven, or brittle, it may indicate that the curing process was either too short or too long. Ensuring quality at this stage helps prevent chipping, peeling, or fading when the fence is exposed to outdoor elements.
Step 3.5: Finalizing Coating Thickness
During curing, the powder coating reaches its final thickness, crucial for balancing impact resistance, flexibility, and weather durability. If the coating is too thin, it may not provide sufficient protection against corrosion, UV rays, and physical damage. Conversely, if it is too thick, it may crack or chip under stress. The correct thickness ensures optimal performance for chain link fencing components, making them highly resistant to long-term environmental exposure and wear.
Powder-Coated Chain Link Fence & Fittings Installation Gallery
Benefits of Powder-Coated Chain Link Fencing
Powder-coated chain link fencing offers superior durability, weather resistance, and aesthetic appeal compared to traditional finishes. The scratch-resistant and impact-resistant coating ensures a longer lifespan, making it ideal for residential, commercial, and industrial applications. Unlike traditional paint, which can chip or peel over time, powder coating bonds seamlessly to the metal surface, protecting against corrosion, rust, and UV damage. Additionally, powder coating provides a range of smooth, matte, glossy, and textured finishes and custom color options, allowing for better design flexibility. It is also an eco-friendly alternative to liquid paints, as it contains no VOCs (volatile organic compounds) and produces minimal waste due to its reusable application process.
When comparing powder coating vs. vinyl coating, powder coating outperforms vinyl in durability and longevity. While both coatings protect against rust, vinyl coatings can crack, peel, and fade over time, whereas powder coating maintains its strength and appearance for years with minimal maintenance. Powder-coated fencing is particularly beneficial for industrial and commercial settings, where high-traffic areas and harsh environmental conditions require a strong, resilient barrier. The combination of low maintenance, cost-effectiveness, and long-lasting performance makes powder-coated chain link fences a preferred choice for security, functionality, and aesthetics.
Key Benefits of Powder-Coated Chain Link Fencing:
- Highly durable and scratch-resistant, reducing wear over time.
- Superior protection against rust, corrosion, and UV exposure for long-term use.
- Customizable colors and finishes for enhanced visual appeal.
- Eco-friendly with no VOCs and minimal waste production.
- Better long-term performance than vinyl coatings, requiring less maintenance.
- Ideal for industrial, commercial, and high-traffic applications where durability is key.
If you have any further questions about chain link fabric, fittings, or the powder-coating process, please don't hesitate to reach out. Our knowledgeable Sales Representatives are always happy to assist you with expert advice, product recommendations, and guidance on choosing the best fencing solutions for your needs. Whether you need help selecting the right coatings, understanding installation options, or exploring customization possibilities, we're here to provide the support you need. Contact us today, and let us help you find the perfect chain link fencing solution for your project.
Contact Us